12 common custom metal fabrication mistakes to avoid
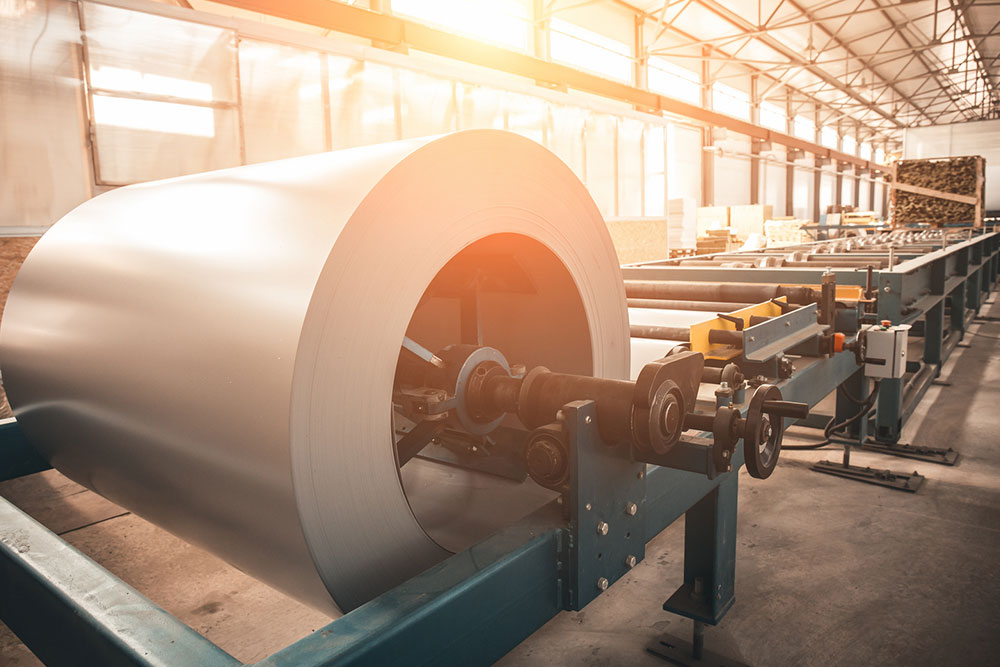
Metal fabrication is a process that involves cutting, shaping, and assembling metal materials to create a final product. Metal fabrication is crucial in numerous industries, like construction, automotive, aerospace, electronics, and manufacturing. This manufacturing method transforms raw metal materials, such as sheet metal, structural steel, and metal bars, into various structures and components used in various industries, from simple brackets and enclosures to complex machinery or metalwork for architectural purposes.
Why customization is better
Custom fabrication stands superior to stock fabrication due to its tailored approach. It allows the selection of materials and methods specifically suited to the product’s intended application. In customization, fabricators consider factors such as stresses, strains, external forces, friction between components, dimensional fit, and surface chemical reactions to make final products. They may then employ two or more methods for increased product efficiency. But it’s important to avoid certain mistakes in custom metal fabrication. These mistakes can compromise the integrity and quality of the final product.
Mistakes to avoid for custom metal fabrication
1. Inadequate planning and design
One of the primary mistakes metal fabricators often make is rushing into the fabrication process without a comprehensive plan and design. Lack of careful consideration of specifications, dimensions, and materials can lead to costly errors. Before starting any project, it is crucial to invest time in meticulous planning and thoroughly document the specifications for clear understanding.
2. Absence of material compatibility
Selecting the right material is pivotal in custom metal fabrication. Fabricators may make the mistake of choosing materials solely based on aesthetics or availability without considering their compatibility with the intended application. For instance, plain steel may erode the product in areas with hard water, so a fabricator should opt for stainless steel instead. Factors such as strength, corrosion resistance, and thermal conductivity can be considered to ensure product longevity.
3. Poor welding practices
Welding is a fundamental aspect of metal fabrication, and improper welding techniques can compromise the final product’s structure. Common welding mistakes include inadequate preparation of joints, improper heat settings, and insufficient penetration. One should hire experienced fabricators with proper welding techniques to ensure durable and reliable metal structures.
4. Improper arc striking
Improper arc striking during welding is another critical mistake that fabricators should avoid. If the arc is struck incorrectly, it can lead to material waste and compromise the quality of the weld. Proper training and adherence to welding techniques are necessary to ensure precise and efficient arc striking.
5. Neglect of safety protocols
Metal fabrication is inherently hazardous, with potential risks ranging from exposure to harmful fumes to the dangers associated with heavy machinery. Neglecting safety protocols can lead to accidents, injuries, and even fatalities. It’s essential to prioritize safety by providing appropriate personal protective equipment (PPE) to fabricators, implementing proper training programs, and strictly enforcing safety guidelines in the workshop.
6. Lack of quality control
A lack of rigorous quality control measures can result in subpar products that fail to meet client expectations. Fabricators should implement a comprehensive quality control process, including regular inspections, testing, and documentation, to identify and rectify any defects or deviations from the original design.
7. No environmental considerations
Environmental factors, such as temperature, humidity, and exposure to the elements, can significantly impact the performance of metal products. Fabricators often make the mistake of neglecting these considerations, leading to premature corrosion or degradation. It is imperative to assess the environmental conditions where the fabricated metal will be placed and select appropriate materials and finishes accordingly.
8. Assumptions about requirements
Working with assumptions is a hit-or-miss issue; wrong assumptions may ruin projects. Communicating the technical requirements of product usage and the environment effectively with fabricators is crucial. Making assumptions about specifications, dimensions, or material preferences can result in a final product that falls short of expectations.
9. Improper material storage
Improper material storage is a common mistake that can compromise the quality of custom metal fabrication. For example, filler materials, especially those used in welding, are susceptible to corrosion. So, storing these materials in dry places is essential to prevent degradation and ensure that they maintain their structure and quality during the fabrication process.
10. Inefficient time scheduling
While fabrication is time-consuming, rushing the job to meet tight deadlines can result in accidents, compromised quality, and errors in the final product. Establishing realistic timelines and prioritizing safety and precision throughout the fabrication process is crucial.
11. Lack of clarity in prints
Lack of clarity in prints, especially in sheet metal fabrication, is a common mistake that can lead to significant errors. Ensuring that critical dimensions, specifications, and details are accurately communicated on the blueprints is essential. This clarity is crucial for both the personnel on the fabrication floor and the engineers responsible for programming the parts to ensure precise execution.
12. Introduction of too many complexities
Overcomplicating the project or overdesigning is a mistake with practical and financial implications. Introducing too many parts, assemblies, or subassemblies can complicate the fabrication process and lead to potential errors. Overdesigning, in particular, can drive up costs without necessarily adding value. Striking the right balance between complexity and functionality ensures a successful and cost-effective custom metal fabrication project.