7 common spray foam insulation mistakes to avoid
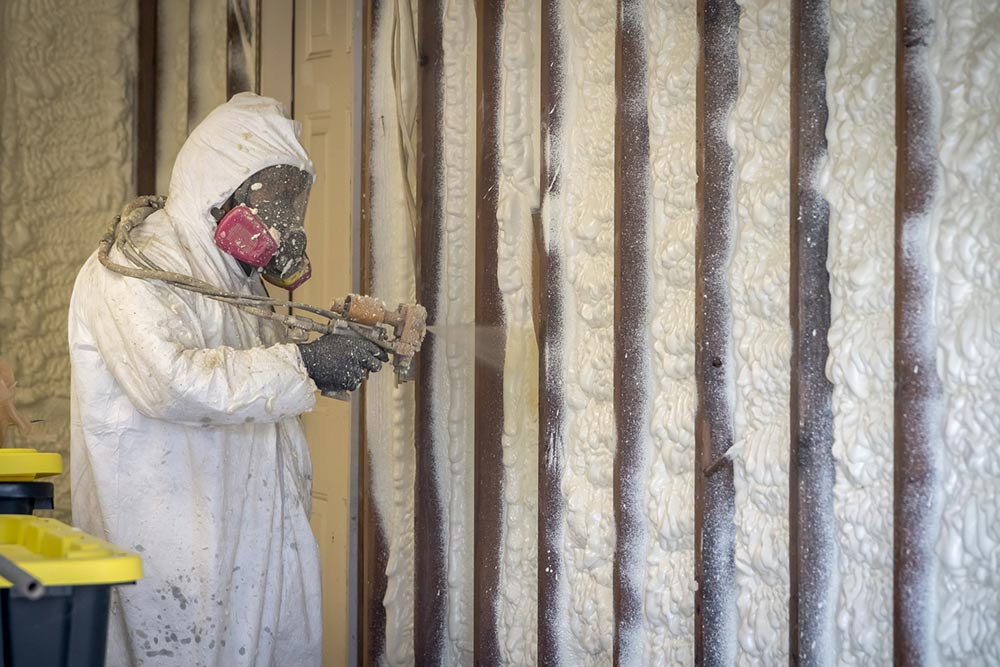
In recent years, spray foam has proven to be a great insulating agent for homes. Like a multipurpose sealant, spray foams also belong to the category of practical repair and renovation tools, making it an ideal choice for homeowners who enjoy DIY projects. However, getting spray foam insulation done is a precision-based exercise, which is why one may make certain mistakes while doing it without professional assistance. Here are some spray foam insulation mistakes one must avoid:
Neglecting proper ventilation
Spray foam insulation tends to be half-baked unless proper ventilation is put in place to sort out certain issues. For example, without proper ventilation, the trapped air in the spray foam insulation layer leads to moisture buildup and condensation. These two problems lead to worse issues like mold growth on the wall and other surfaces where this insulation layer is applied. Mold growth not only compromises the insulation but is also incredibly unhygienic and can cause health issues for the occupants living or working in such a property.
Heating the canisters too much
Many people who apply spray foam insulation on their own believe that high temperatures on the canister will speed up the application process. However, this is a wrong notion. One must not heat the canisters beyond 100 degrees as that creates a risk of the canisters blowing off their caps and causing a huge, foam-filled mess all around. Ideally, the canister should be at room temperature when spraying it.
If the insulation foam is being used in a place with cold temperatures, then one can use water tubs and multiple canisters to keep the foam from freezing.
Using incorrect thickness
Spray foam insulation works best when the person applying it uses the correct amount of material to create a thick insulation layer. Finding the right balance is key, as applying too little will lead to inadequate insulation (and creates air gaps and air seals), while spraying too much wastes resources and unnecessarily increases costs.
Understanding the perfect balance helps people set a budget, purchase just the right quantity of foam, and apply it most efficiently to create the layer. One can check credible sources online or consult with professionals to learn more about finding the right balance for one’s home or workplace. Reliable sources can provide information on the optimal thickness for achieving a great insulation performance.
Not wearing personal protective equipment (PPE)
The spray foam particles are harmful to one’s health. Many health issues can arise from spray foam particles. For instance, mistakenly consuming it can cause a host of gastrointestinal issues, while breathing in the particles can lead to choking or breathing problems.
To avoid such problems, taking all the right precautionary measures is essential. Firstly, it is advisable for people to hire a contractor or other professional to do the job. This protects the property owner from harm and ensures that the professionals take all the safety precautions from their end so their health is not endangered.
If property owners or managers intend to do the spraying by themselves, they must wear personal protective equipment (PPE), complete with respirators, gloves, and goggles, to not let even a single particle inside their eyes, nose, mouth, ears, and other parts of their face or body.
Spraying the product too quickly
All DIY tasks require patience and precision and spray foam insulation layer creation is no different. Hastiness in this process leads to issues like the creation of air gaps in the walls and other areas on which the spray is coated. This severely reduces the efficiency of the spray foam and makes the surface look ugly from an aesthetic point of view. To avoid these problems, it’s important to spray the foam slowly and carefully to create a smooth, effective insulating barrier.
Also, if one goes ahead and does the task quickly and recklessly anyway, they can still get a contractor to provide touch-ups to their work and fill in all the gaps at a reasonable expense.
Neglecting moisture control
Moisture is a major detriment to all insulation materials and systems. Therefore, one must address all the issues that come with moisture during spray-foam-insulating a place. Moisture trapped within walls is a major source of mold growth and poor insulation after spray foam material is applied on a given surface. One can use various moisture removal techniques and even call mold removal services to get the job done before starting the insulation process.
Not mixing the spray foam insulation chemicals properly
Getting the mix right while melding two or more chemicals to create a spray foam insulation layer is key to how strong, durable, and reliable the layer will be when it is applied on walls or other surfaces. People tend to get the percentages and proportions wrong when they mix the chemicals by themselves without checking any manual or consulting a professional for the same. This results in the forming of poor foam and, by extension, poor insulation when it is applied onto surfaces. Ideally, getting the job done by a professional can solve this problem and save a lot of time for people.
Some of the other mistakes that people make include choosing spray foams with odor and off-gassing, failing to seal gaps and cracks, and using a latex paint sprayer.