7 tips for industrial machine maintenance
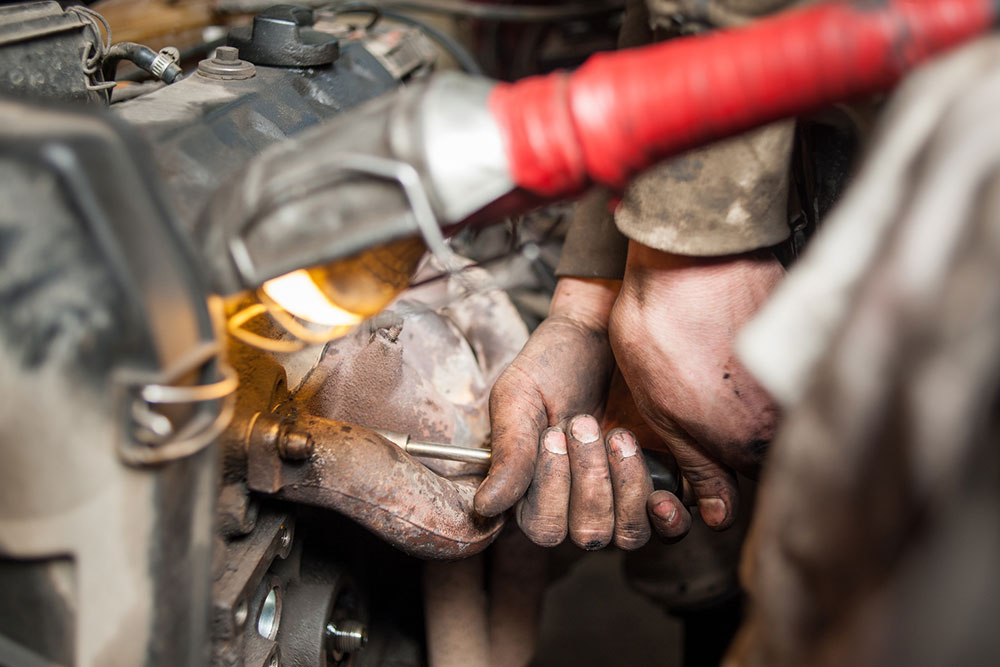
Industrial machines have moving parts and require regular maintenance to ensure they meet the safety criteria to prevent mishaps at the workplace. Inspections, replacements, and repairs should be carried out regularly to detect any abnormalities, which could make it easier to resolve issues before any significant damage. For those who oversee such projects or sites in an industrial setting, following certain machine maintenance tips can help ensure their safety and that of everyone around them.
1. Inspect safety features regularly
Every machine, especially industrial equipment, comes with a series of safety features. A few include warning signs, guard rails, alarm systems, and emergency shut off. One needs to be mindful of these safety features to avoid accidents in the workplace. Furthermore, the individual should check if the features work properly and address any issues immediately. If any of the warning lights turn on, they must not be ignored. Regular inspections involve taking a look at each part of the machine, including large and tiny components. Even a part that is a little loose or has more play than needed could lead to an accident.
2. Clean machinery periodically
An essential tip when handling machinery of any kind is to clean it regularly. Dirt and debris usually accumulate on industrial machinery, resulting in the wear and tear of the equipment. Moreover, corrosion, retaining rings, and rust are other complications that may arise with regular use. Together, these factors pose a risk to the machinery and cause it to malfunction and endanger one’s safety. So, one must clean each component thoroughly, including the joints and smaller sections of the machine that might get overlooked. Applying a rust-preventing coat on all the exposed metal areas will also help enhance the machine’s life. One should also speak to a professional when it comes to cleaning more complex parts of the machinery.
3. Ensure lubrication
While this might seem like a tiny step in the cleaning process, it is the most crucial thing to inspect. There is constant friction in a moving machine, and the lack of lubrication could increase the wear and tear, adding to repair costs in the long run. Proper lubrication of each part will ensure that the machine functions efficiently and wears out gradually, as expected. Following this step will also help avoid any delays in production and delivery. A few places to check lubrication before starting the machine include motors, high-speed spindles, and other parts, as indicated by the manufacturer. It is also essential to use the right type of lubrication for different components of the machine to keep them functioning well.
4. Perform calibration checks
Each machine will require calibration checks every few weeks or months based on the type of work carried out. Such checks ensure that the work rendered is precise and without any faults. The ideal way to determine if the check is required is to speak to the manufacturer and follow the guidelines suggested in the user’s manual, along with the recommended calibration process and timeline. Moreover, having a professional technician assigned to these machines is crucial as they could provide regular service to ensure constant wear and tear does not affect the machine’s full potential. If there are faults in various components, the technician can easily take care of them in time and prevent mishaps.
5. Solve issues in real-time
There’s a lot that can go wrong with industrial machinery irrespective of how fresh its parts or project are. However, if a problem occurs, one must solve it in real time. Leaving the error unattended could lead to other complications and compromise the safety of those working in the area. So, it is crucial to follow protocols when dealing with machinery maintenance, repairs, and replacements. Note that while the cost of resolving the issue might be high, leaving it unserviced could lead to greater consequences that can endanger people working in the factory. Further, the lack of effective maintenance could also lead to legal trouble that carries heavy penalties.
6. Check machinery that is out of use
Several pieces of machinery at a workplace might be kept on standby for months or years to handle heavier workloads. But before using them, one should ensure they are inspected for any issues and if they can still render quality work. Conduction and inspection will ensure that any issues are addressed and resolved even before the project begins and prevent any delays in the future. A professional might also need to recalibrate the machine if the task requires it. So, one should always be prepared for any scenario.
7. Maintain a log
While one might carry out all the necessary checks, repairs, and replacements, one should always remember to maintain a log of what work was done. The log should include details of the machine’s usage, its last maintenance, and other crucial details that could help troubleshoot any issues in the future. The log should also include any issues that were experienced during the use of the machine, which helps warn the operator to be careful and vigilant of potential problems. Each log should include the date and name of the person using the machine, which could have valuable insights that could help the maintenance process.